MRO Management magazine recently interviewed Nick Hope, Business Development Specialist, Intoware to discover why MRO digitisation is essential, and what makes the MRO sector the perfect space for WorkfloPlus to deliver efficiency gains.
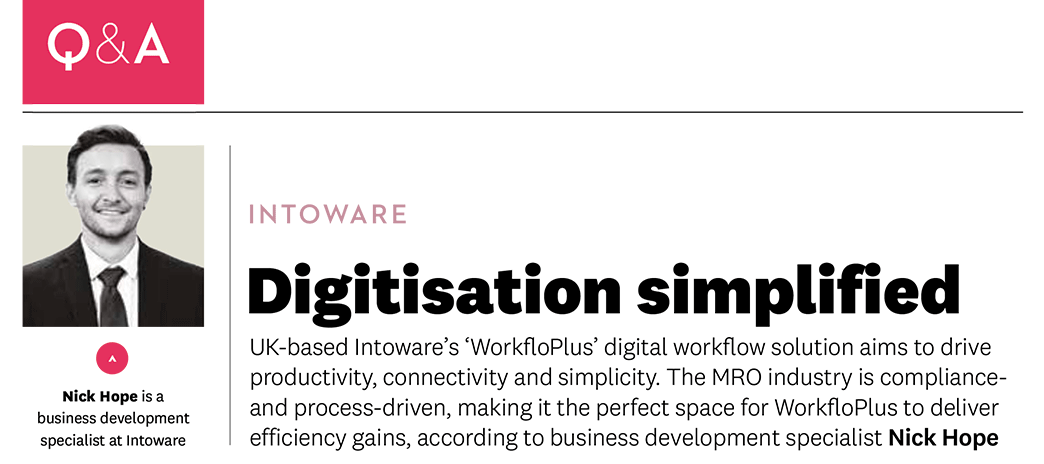
MRO Management: What does Intoware offer and how did your ‘WorkfloPlus’ platform come about?
Nick Hope: Intoware developed WorkfloPlus to help companies digitise their processes so they can standardise procedures and streamline operations. It means companies can move away from paper-based forms – whether that’s inspections, maintenance, repairs, health and safety, quality control or auditing – and carry out these tasks digitally via mobile, tablets or AR wearable devices. WorkfloPlus enables frontline engineers and technicians to focus their efforts on the job at hand rather than the more mundane admin side of things. The platform also automatically generates a digital log of the entire process which is invaluable for auditing and compliance reporting.
How would ‘WorkfloPlus’ be used in the commercial aviation MRO industry?
WorkfloPlus is perfect for the MRO industry and offers numerous benefits. Not only will it provide the user with digital instructions that guide them through the correct way to carry out a task, but it also records any issues they face and captures photo or video evidence to confirm the problems.
There’s also the option to include assets into workflows such as training videos, detailed drawings or PDF reports to ensure a technician has all the information they need to carry out a process accurately, as well as supporting upskilling and training.
Then, when you have completed your process WorkfloPlus automatically generates areport, so you save the time traditionally spent on inputting data as well as removing the chance of human error.
The information captured can be transferred to where you need it to be to make the best use of the data generated. Whether that’s an ERP system or live visual data dashboards such as PowerBI the management team will always have an accurate view of what’s happening on the ground.
With data collection and reporting happening in real-time, repairs and maintenance operations can take place as quickly as possible without having to worry about the admin. WorkfloPlus helps technicians work more efficiently with less downtime or losses in productivity.
In addition to the automatically generated audit trail, it’s also possible to include questions in the workflow to check compliance issues or health and safety standards are being met, such as, ‘Do they have the correct PPE orTools?’. If the answer is ‘no’ or they can’t provide photo evidence, the workflow will advise them to stop and come back to the task. All of which is recorded in the report.
Technology and regulations in the aerospace industry are constantly evolving and that means so are the processes. WorkfloPlus enables those changes to be implemented quicker than ever before. By simply updating the workflow it’s possible to instantly roll that change out across the whole organisation so every technician is always working to the latest more efficient method of completing atask.
Was WorkfloPlus developed with the MRO industry in mind?
Historically we concentrated on four sectors: Oil & Gas, Manufacturing, Utilities and Infrastructure, but following success in those areas and some fantastic engagement at trade shows we have often been approached by customers from MRO. Our customers in these other sectors face many of the same problems as those seen in the MRO industry and also operate under heavily regulated and compliance-driven conditions, which is why WorkfloPlus lends itself perfectly to the MRO industry.
Following conversations I’ve had with MRO companies I immediately understand the crossover with our existing WorkfloPlus users. The importance of reducing costs without compromising on quality is something I talk about every day with our customers.
I’m also seeing a move towards departments across a range of industries involved with Process Improvement, this is a key area for MRO. Say for example, you have an employee that has been with the company for five or ten years and naturally they have become very efficient in their role, with WorkfloPlus you can document their more effective method of carrying out a process and provide that to the rest of your team, whether they’re in the next room or on the other side of the world.
WorkfloPlus also identifies where potential improvements can be made through the various metrics that it provides. The reports will show exactly how long each step in a process takes a technician to make, therefore you are able to continuously adapt, change and improve processes where necessary as well as identify any potential training needs across the team.
What differentiates WorkfloPlus from other digital tools being offered and used in the industry?
There are a lot of digital workflow platforms available, but many just create digital lists to replace existing paper forms. WorkfloPlus actually ‘digitalises’ an entire process and generates valuable data that can be used to make data-informed decisions. It’s not only about knowledge capture and process capture, but also where it goes and where it’s stored, how we integrate that with systems, and how we interrogate it – such as with the dashboards – and this drives data-driven decision making in real time.
WorkfloPlus can automatically notify the relevant person when there is an issue to reduce downtime, for example if a technician identifies a fault, the system can automatically inform the repairs team. Which means repairs take place as soon as possible without the need for extra admin which increases the productivity of the whole team.
We also take pride in the way we evolve the features within WorkfloPlus. We work in partnership with our customers and listen to their needs. In fact, many of the features available today have come about as a result of wanting to add extra value to the user - one of the many benefits of having an in-house development team.
Can you outline any success stories from other industries the digital platform is used in?
In the pharmaceutical industry, manufacturer Bayer adheres to strict quality and regulation guidelines known as GxP. The process for cleaning down their machines between production of different product lines was previously paper-based and required a manual 2 step validation upon completion. This is now digitised using WorkfloPlus and a 40 per cent time reduction has been realised which has resulted in a long-standing partnership with Intoware.
In the Oil and Gas industry one of our customers has experienced a 300 per cent increase in productivity. A company that maintains offshore assets has been able to increase inspections from 8 to 32 inspections per day, with manual data entries now digitised and no time delays between engineers flying to and from those assets who would previously have entered the information gathered back at headoffice.
Have there been any barriers to implementation identified by potential customers in the MRO industry in discussions you have had so far?
There are no barriers, but data security is a large consideration in the MRO industry and is often the first question raised. To digitise processes that relate to either military or sensitive equipment, customers need to know that the data being captured is safe and secure. To satisfy this, WorkfloPlus can be hosted within a customer’s private cloud environment whether that be Azure, AWS or any other upon request, or we an also offer hosting ourselves on a Microsoft Azure Shared Cloud environment. We are also ISO27001 certified (aninternational standard to manage information security), but also, we adhere to standards set by OWASP meaning we build software securely and follow best practices from a security standpoint.
How widespread do you expect MRO industry usage of WorkfloPlus to become?
Aviation and MRO is a big growth area for us, and our involvement in the industry is increasing with WorkfloPlus being well received by a number of the big players. We will be attending industry related events throughout 2023 and are very excited to get going and meet new prospects.
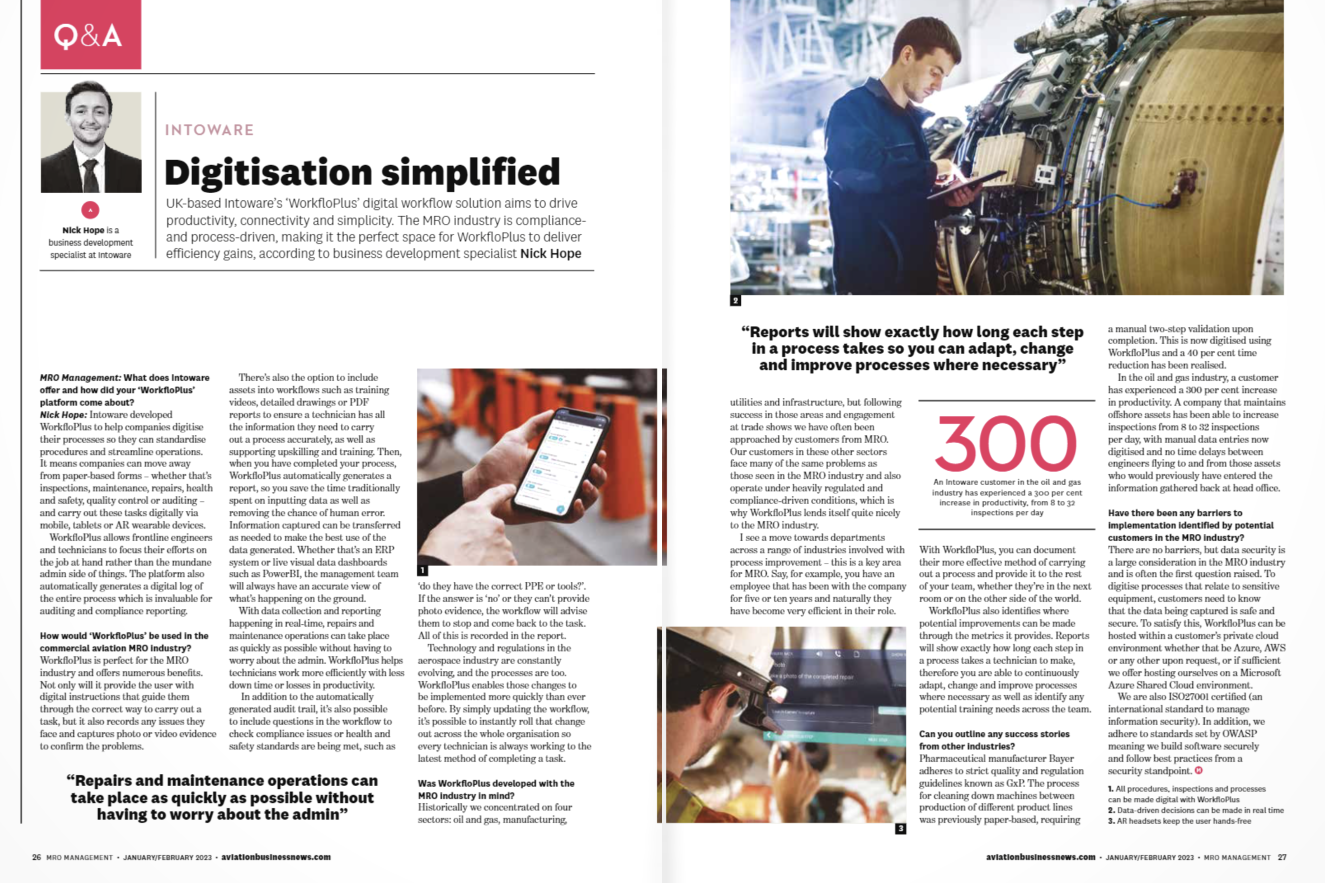