Anyone involved in manufacturing will have heard of Industry 4.0, the powerful concept of bringing smart technologies such as the Internet of Things (IoT), cloud computing, analytics, AI and machine learning to manufacturing. At the core of this revolution is the need for greater efficiency, productivity and quality.
These ‘smart factories’ generate data from production operations and combined it with information held within ERP systems to create greater visibility than was previously available in the siloed data held in spreadsheets or legacy, paperbased systems.
Smart factories show you how your plant and machinery can be streamlined to get the most from your equipment, but do your current systems also show you where all the human bottlenecks are that take up time and resources? How do you ensure that the human element of your smart factory is also working to its optimum?
Evolve and embrace Industry 5.0
Industry 5.0 is all about putting your people at the centre of the production process, so you have a clearer understanding of the problems they have in their work routines and how to solve them. It unleashes the hidden big data possibilities of your human process. It’s about putting people first and being ‘data-informed’, not just ‘data-led’.
New technologies such as smart digital workflows, assisted reality (AR) and the cloud can improve human process efficiencies, reduce costs, ensure your staff are safe and speed up staff onboarding and upskilling. By automating paper-based and legacy processes, you can bring your frontline workforce into your big data picture to help you:
- Harness data from human processes
- Ensure auditability and traceability across all operations
- Reduce human errors and improve productivity, for better business performance
- Provide ‘real-time’ data and reporting to improve the quality of work and deliver cost efficiencies
Putting people first
But while the need to optimise factory processes is essential, this isn’t enough on its own. To deliver great performance, you must put people first – from frontline workers to supervisors and managers, they need to be at the centre of your operations. The real power behind any digital transformation is the people, as they will help to drive change.
The most successful digital transformations are when people, processes and systems are combined harmoniously. Tailored digital workflows enable processes carried out by humans to be easily collected and analysed. Every step of a task is easily recorded so you can see where the ‘human bottlenecks’ are in your manufacturing processes – are the best people on the job, are they being supported in the right way?
If you can allocate the right number of skilled people to reduce inefficiency and enhance productivity you can prevent these sticking points. Also, by supporting people with the right training when it’s needed on the factory floor with standardised, guided workflow instructions, they will quickly learn their role inside and out. Workflow automation software can highlight the human elements, that a smart factory often misses.
Industry 5.0 in action
A ‘real-life’ customer, Bayer Pharmaceuticals has successfully digitalised its factory operations with workflow automation platform, WorkfloPlus to help streamline production change overs at what is considered to be one of the most advanced manufacturing plants in Italy.
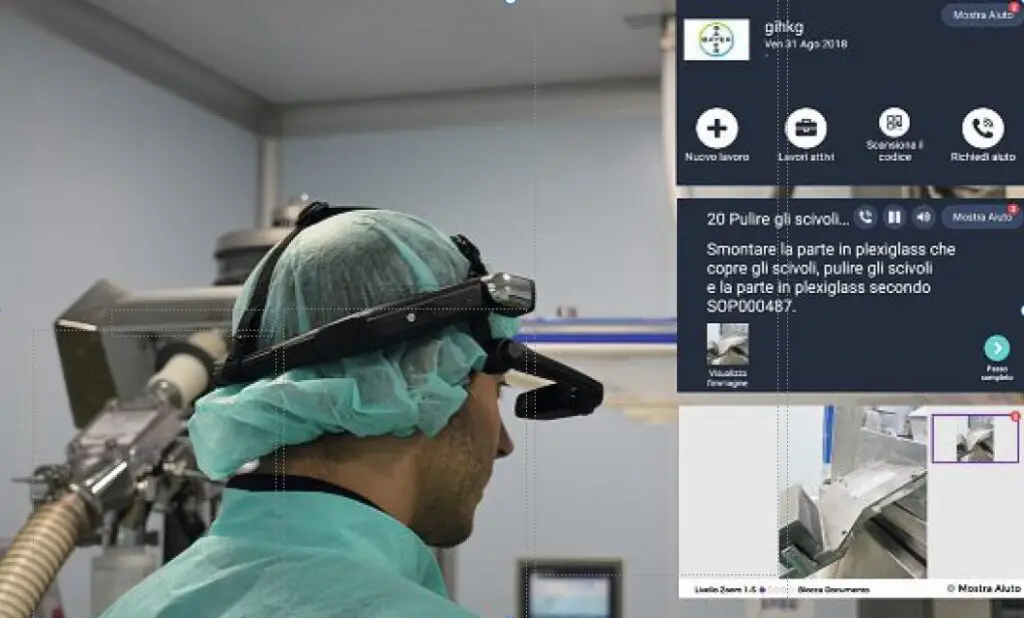
Bayer Pharmaceuticals deployed WorkfloPlus with Realwear wearable devices to streamline and manage its essential production changeover process, in the highly regulated pharmaceutical market. Drug manufacturing operations require regular cleaning and changeovers between each batch, by adopting WorkfloPlus it allowed frontline factory workers to ensure that the procedure is taken in a consistent and timely manner, minimising ‘downtime’ for greater cost efficiency. At the same time, guided work instructions ensure thorough audit checks that satisfy GxP (good practice) compliance needs better than any paper ‘tick-list’ could deliver.
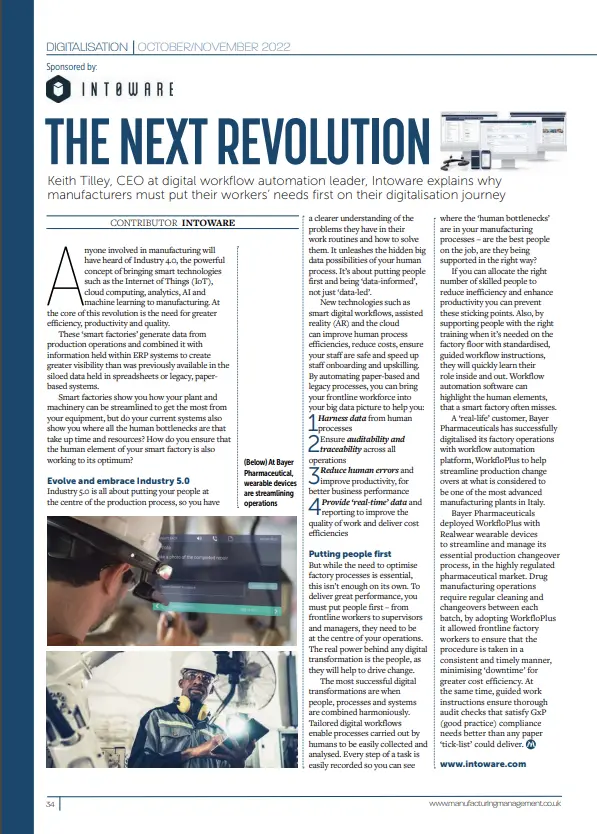